射出成形の不良原因と対策|設計・金型・成形条件の最適化
射出成形は製造業で広く使われる手法ですが、ヒケやソリ、ショートショット、バリなど様々な成形不良が大きな課題となります。これらの不良は製品品質低下や歩留まり悪化を招き、手直しと選別コストも発生します。不良は事後対応よりも予防が重要であり、材料特性、製品設計、金型構造、成形条件など複数の要因を統合的に管理することが必要です。
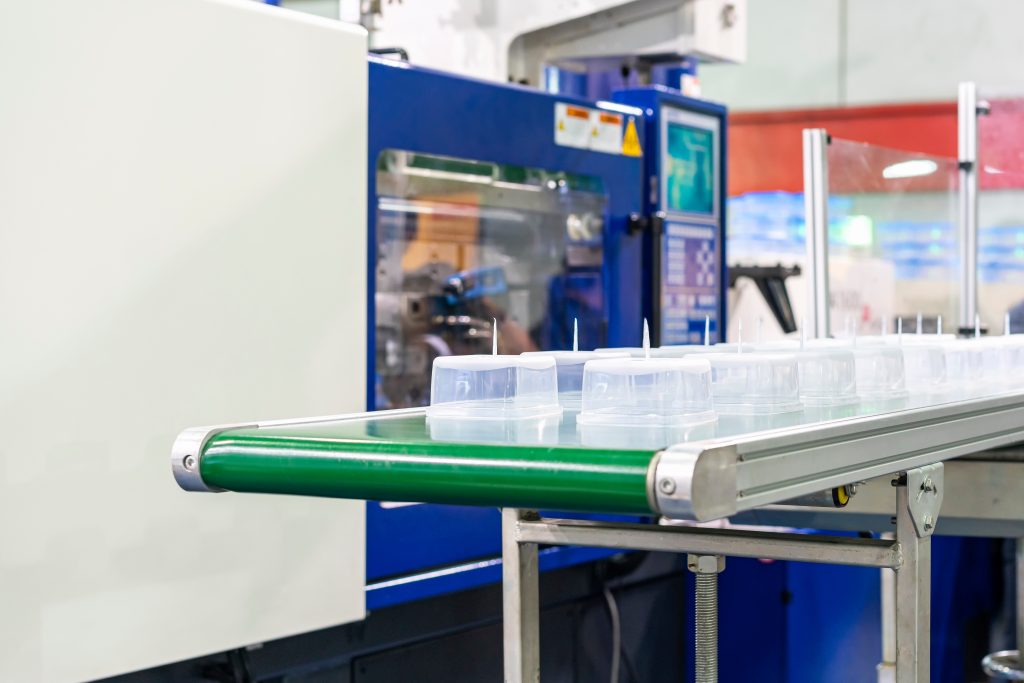
射出成形における成形不良とは
成形不良とは、射出成形などの樹脂成形において、製品の外観や性能に不具合が生じる現象を指します。バリやヤケ、シルバーストリーク、ヒケ、ボイドなどがあり、品質や機能に影響を与えます。成形不良の原因は、樹脂の性質や成形条件、金型や機械の状態など多岐にわたります。些細な要因によって不良が発生するケースもあるため、適切な管理と対策が不可欠です。歩留まり向上やコスト削減の観点からも、成形不良をいかに防止するかは重要度の高い課題といえるでしょう。
成形不良の種類と原因
バリ
金型の合わせ目などから樹脂が漏れ出し、余分な突起ができること。型締力不足、金型の摩耗やガタつきが原因。
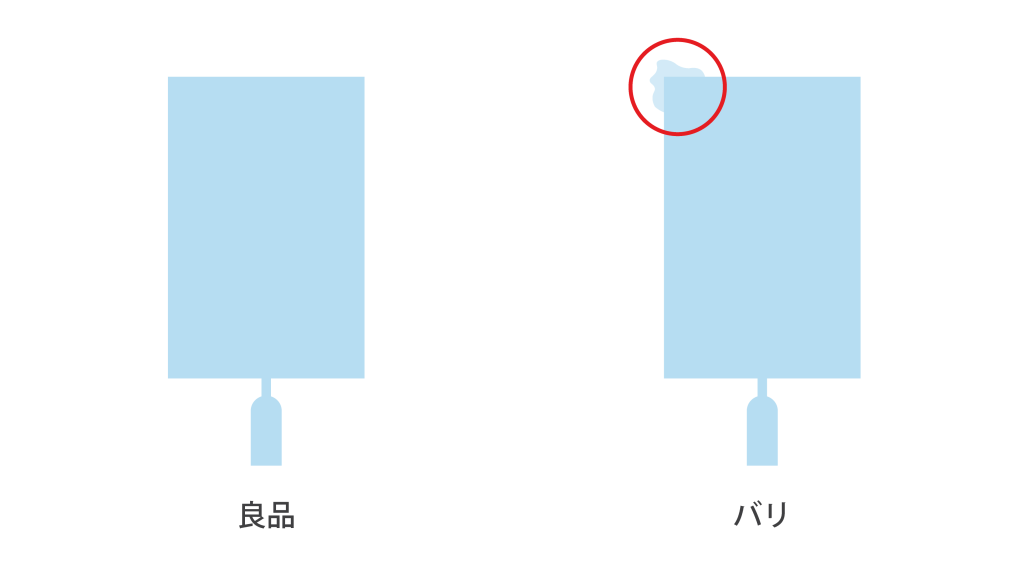
ヤケ
樹脂が過熱され、焦げたような変色や臭いが発生すること。樹脂の滞留、射出速度が速い場合に発生。
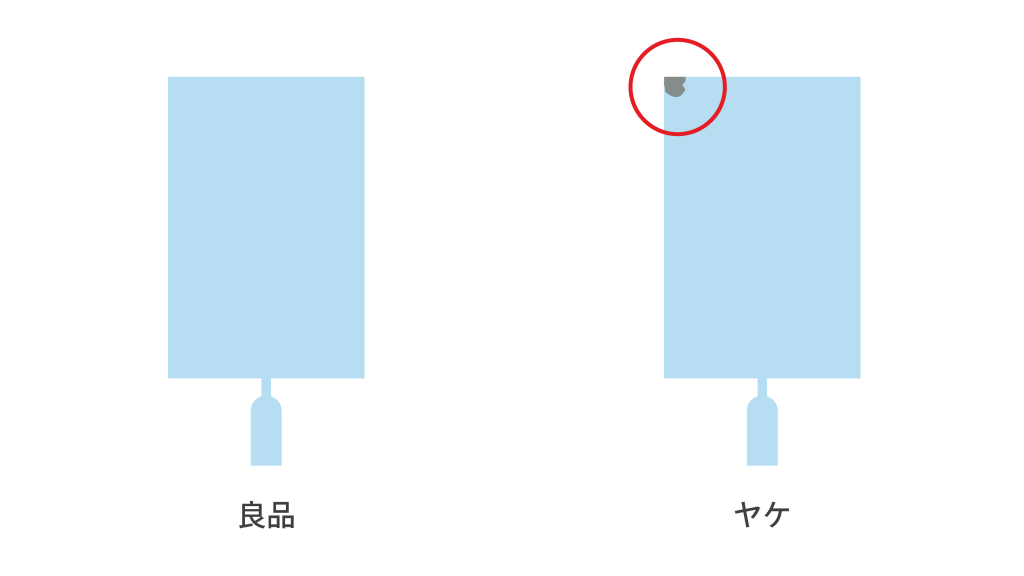
シルバーストリーク
樹脂内の水分や揮発成分が蒸発して、銀色の筋状痕が生じる現象。樹脂内の水分やガスの残留によって発生。
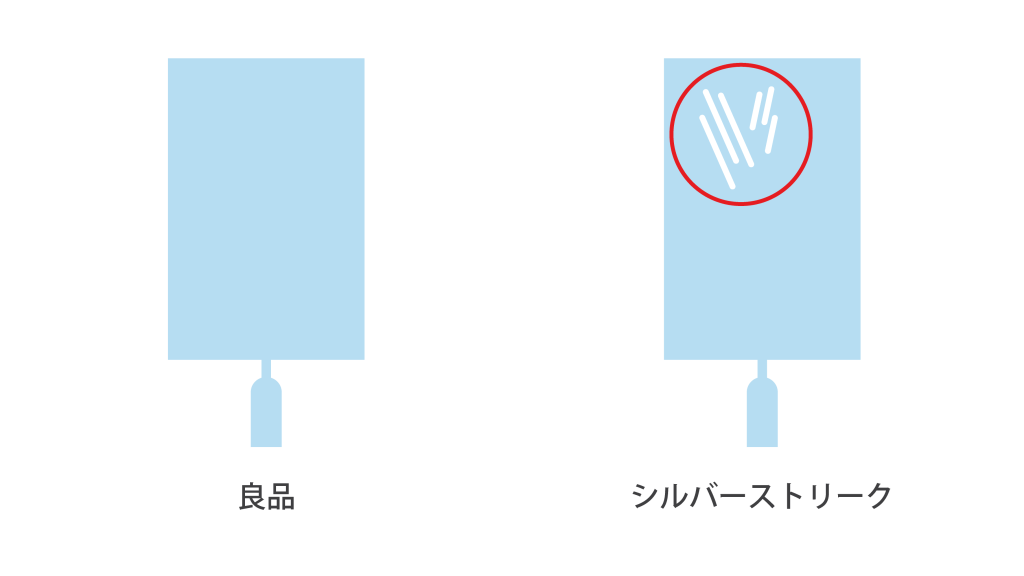
ヒケ
肉厚部の体積収縮により、表面が凹みが生じる現象。主な原因は肉厚設計の不均一、冷却不足によって発生。
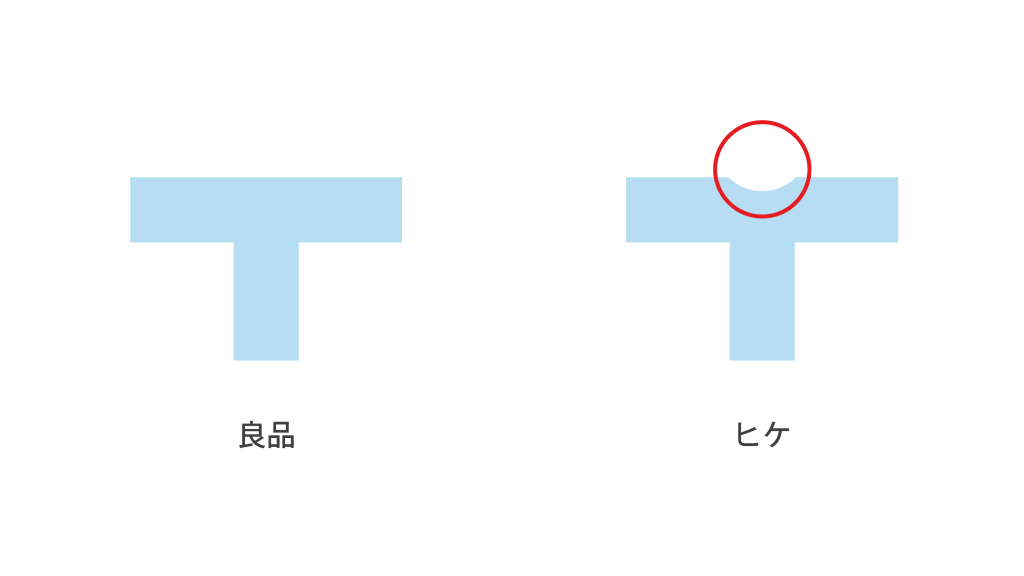
ボイド
成形品の内部に気泡や空洞が発生する現象。冷却不十分、射出圧力不足、ガス閉じ込めなどが原因。
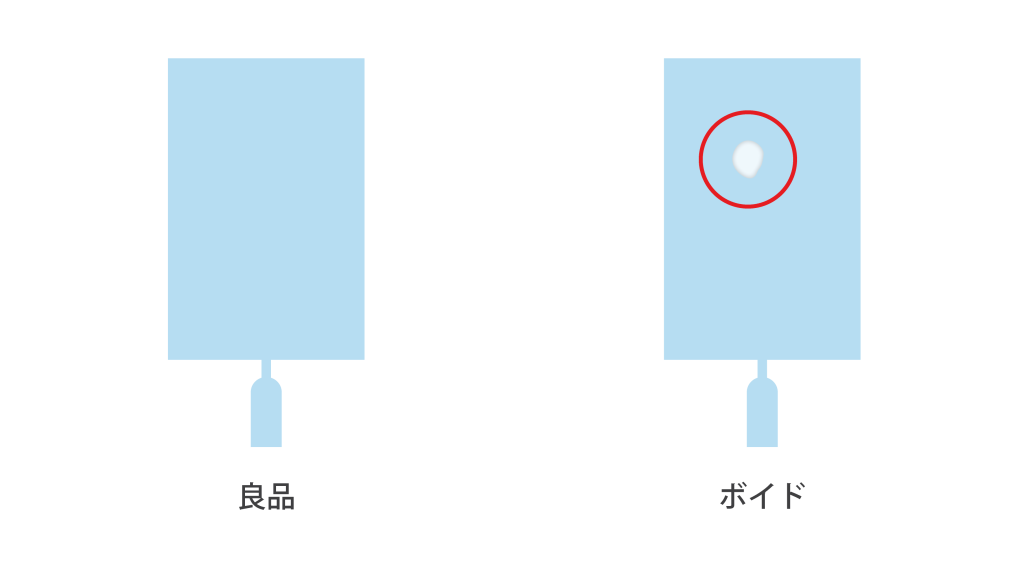
ショートショット
樹脂の充填不足により、製品に欠けた(欠肉)状態ができること。射出圧力・速度の不足、金型温度の低さが原因。
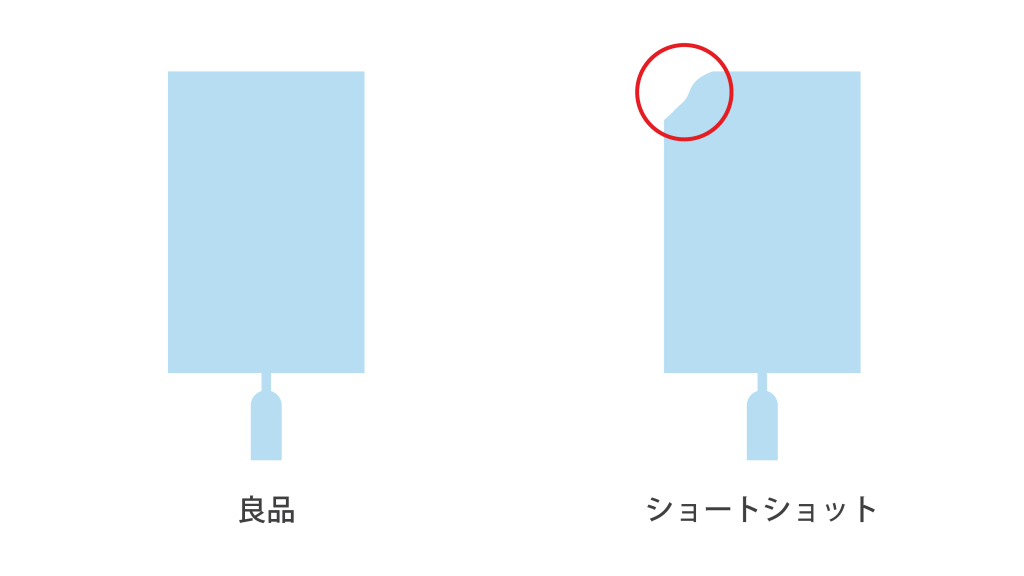
ソリ
成形品が反ったり歪んだりする変形現象。冷却の不均一、肉厚差、残留応力などが原因。
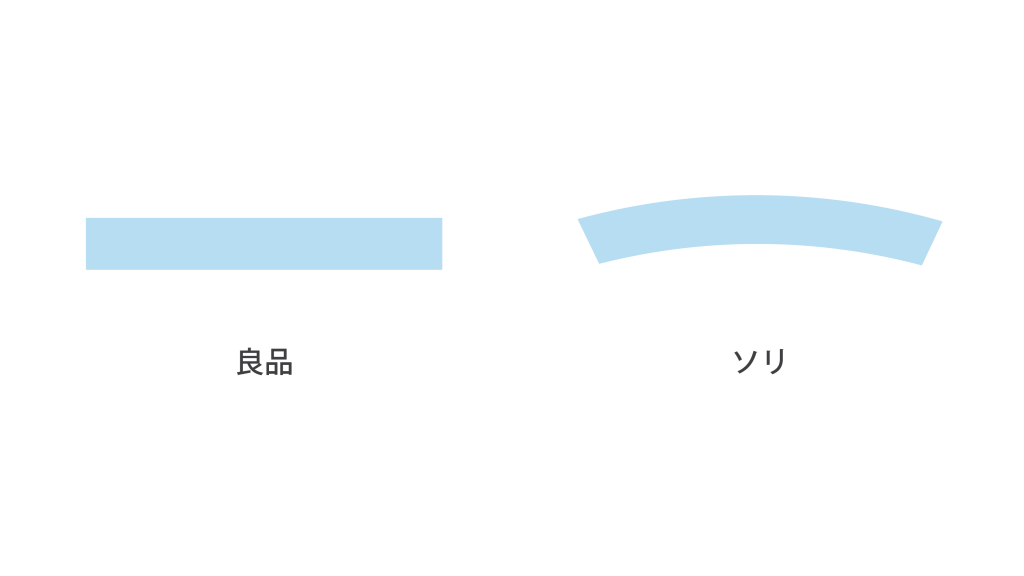
クラック
成形品に生じた割れや亀裂のこと。成形条件の適切でなかったり、離型時の応力集中などが原因。
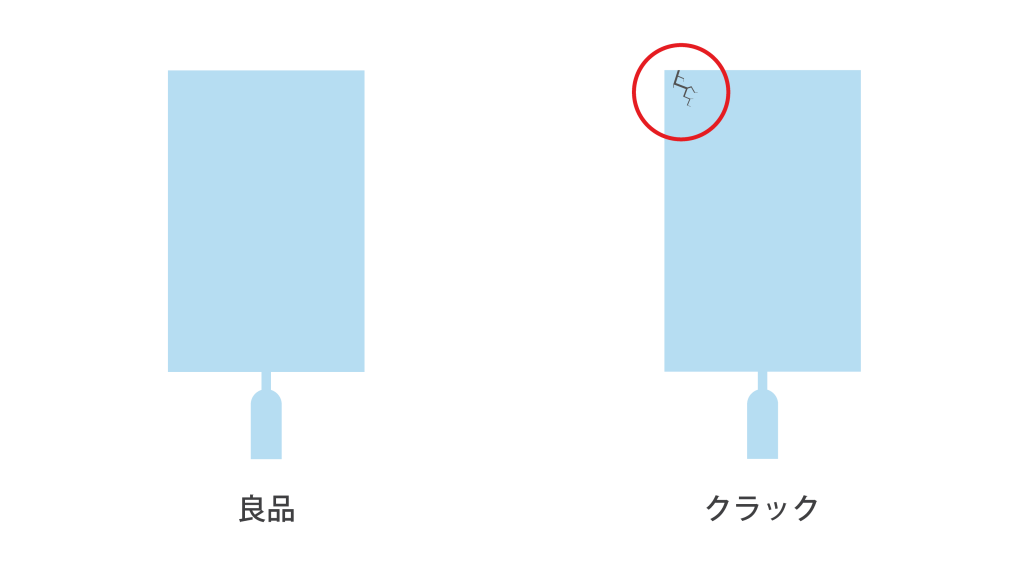
ウェルドライン
複数の樹脂が合流する部分にできる線状の跡。樹脂温度や金型温度が低いか、流動方向の設計不良が原因。
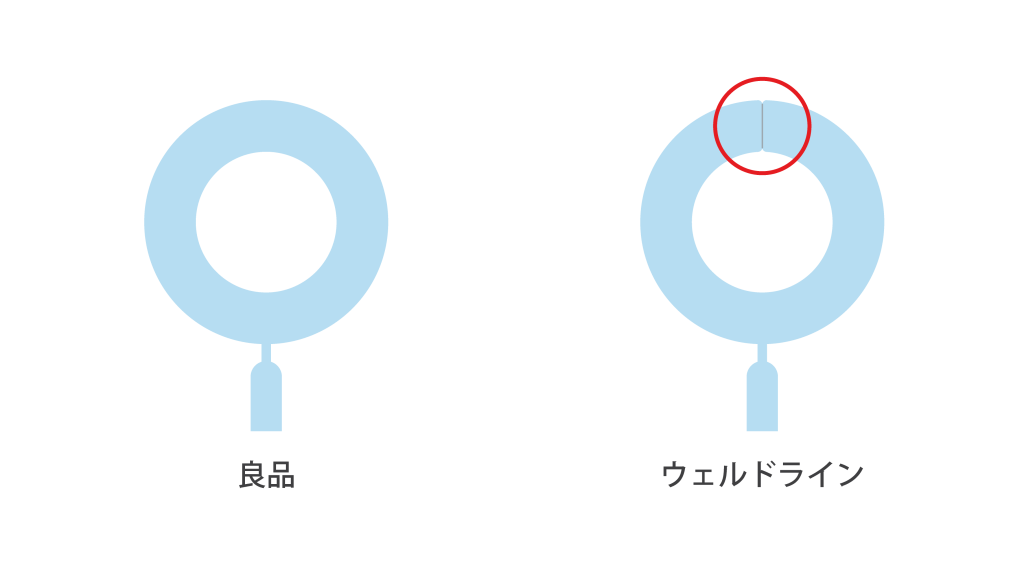
ジェッティング
樹脂が勢いよく流れて、成形品に蛇行した模様ができる現象。ゲートの設計不良、あるいは射出速度が速すぎる場合に発生。
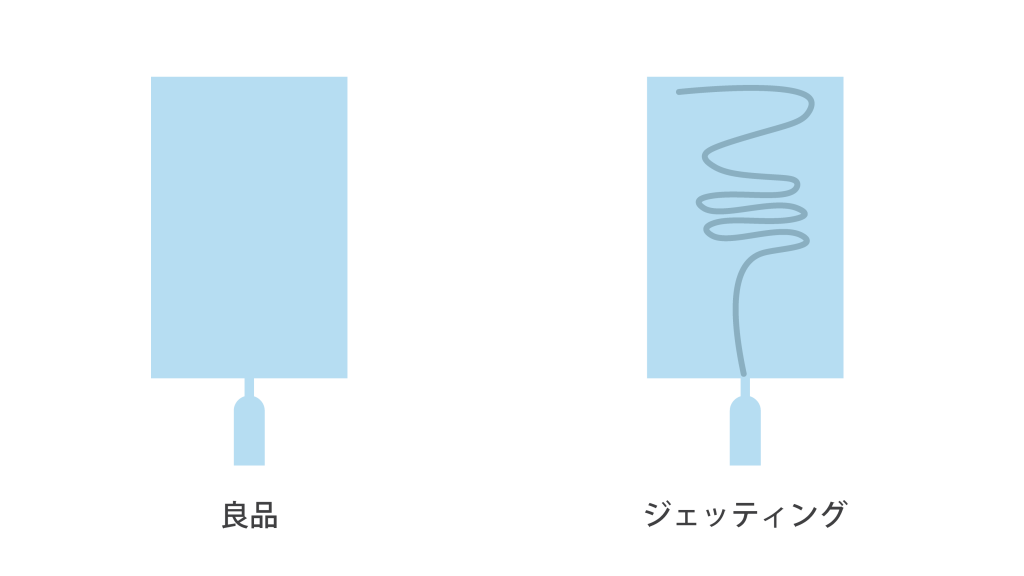
フローマーク
樹脂の流動した痕が表面に残り、波状模様が現れる現象。樹脂温度や金型温度が低い、または射出速度が不適切な場合に発生。
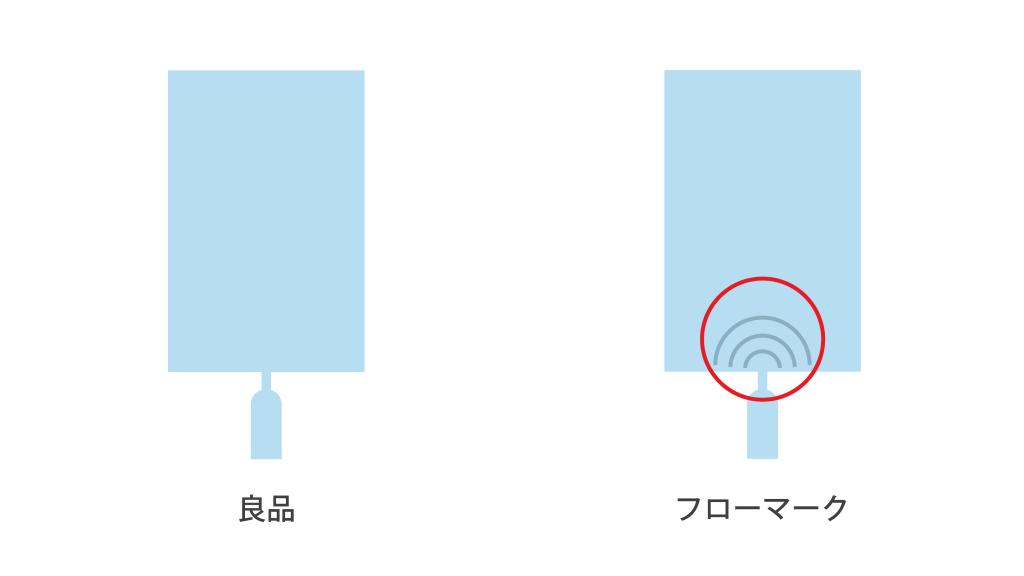
成形不良の対策
射出成形の成形不良をなくすには、製品設計時に不良発生リスクを低減することが重要です。ここでは、設計段階での成形不良予防策として、肉厚設計、抜き勾配、ゲート位置最適化、パーティングライン設定を解説します。
肉厚設計
対策対象の不良:ヒケ・ソリ(反り)・ウェルドライン
成形品の厚みにバラツキがあると、成形不良が起こりやすくなります。壁厚を均一に保ち、急激な厚みの変化を避けることで、冷却収縮の差によって発生するヒケやソリを防止することが可能です。厚肉部に肉盗み(部分的に凹ませたり中空構造にしたりすること)を施すほか、リブで強度を確保しつつ、厚肉部を減らしてヒケを抑制する方法があります。しかし、リブが厚いとかえってヒケを発生させてしまうことにも注意が必要です。
抜き勾配(ドラフト角度)
対策対象の不良:離型不良(キャビとられ)・スレ・白化・変形・クラック
成形品が金型からスムーズに抜けるよう、垂直方向の面には抜き勾配(ドラフト角度)を設けます。一般的には、成形品はコア(可動側)に残る設計とします。これは、可動側にはエジェクタピン(突き出しピン)を設けることができ、成形品の取り出しがスムーズになるためです。 キャビティ(固定側)には十分な抜き勾配を設け、製品がコア(可動側)に残るように設計することが重要です。抜き勾配が不十分だと離型時に「キャビとられ」(製品が固定側に残る不良)が発生するほか、スレや白化、キズ、場合によってはクラック(割れ)などの不良につながることがあります。
ゲート位置の最適化
対策対象の不良:ショートショット(充填不良)・ウェルドライン・フローマーク・ボイド(気泡)・ソリ
ゲート(樹脂の流入口)の位置やサイズが不適切だと樹脂の流れが偏り、充填ムラや圧力分布の不均一を招きます。製品全体に樹脂が行き渡りやすい位置にゲートを配置し、必要に応じてゲート数を増やしたり位置を工夫したりしてウェルドライン(融着不良が原因で、成形品の表面に入る筋)が重要部に出ないようにします。設計段階でCAE流動解析を活用し、樹脂の流動挙動をシミュレーションするのも有効です。
パーティングラインの設定
対策対象の不良:バリ・外観不良・エジェクタ痕の目立ち
金型の合わせ面に段差や隙間があると、そこから樹脂がはみ出してバリが発生します。製品の外観に影響しにくい位置にパーティングライン(PL面)を設定し、エジェクタピン(突き出しピン)の跡が目立たないよう裏面側に配置する構造にします。PL面の精度維持やメンテナンスもバリの防止に不可欠です。
金型設計における不良防止のポイント
射出成形の金型を設計する段階から、成形不良の抑制を意識することが重要です。特に、以下の5つのポイントを留意してください。
冷却系統の見直し
金型内の冷却回路の配置が不適切だと、温度差が大きくなる箇所が発生し、部位ごとに樹脂の冷却収縮量が変わってソリ(反り)や変形が起こります。特に平板形状の成形品では、上下の金型温度差が生じないようバランス良く冷却回路を配置することが重要です。
ガス抜き(エアベント)の設計
樹脂充填時に金型内の空気やガスを適切に逃がすことができない場合、圧縮されたガスが高温になってヤケ(ガス焼け・焼け焦げ)が発生したり、充填不良の原因になったりします。金型の最終充填部やガスの溜まりやすい箇所に微細なすき間や溝を設け、空気が外部に抜けやすいエアベント構造を設計しなければなりません。
金型精度の向上
型締め時に合わせ面に隙間がないよう、金型フレームや型板の剛性を十分に確保し、高精度に加工・組み立てします。合わせ面がわずかでも浮いていると、成形時の樹脂圧力で隙間から樹脂が漏れ出しバリが発生します。
ゲートやランナの設計
樹脂ごとの流動性に適したゲートサイズ・形状を選定し、充填バランスを考慮してランナ径・長さを設計します。ゲートが小さすぎるとショートショット(充填不足)や偏肉を招き、大きすぎると過剰充填につながりバリが発生します。
エジェクタピンの配置
十分な数のエジェクタピンを適切に配置し、製品を偏りなく押し出せるようにします。ピンの配置が不適切だったり本数が足りなかったりすると、離型時に製品が変形してソリ(反り)や白化といった成形不良が生じることがあります。適切なエジェクタピンの数は、部品の構造や射出圧力、金型キャビティ面積などから見積もりが可能です。
成形条件の最適化による不良予防
成形条件を見直すことによって、不良の発生を予防できます。ここでは、射出圧力と速度、保圧と保圧時間、樹脂温度と金型温度、材料管理について解説します。
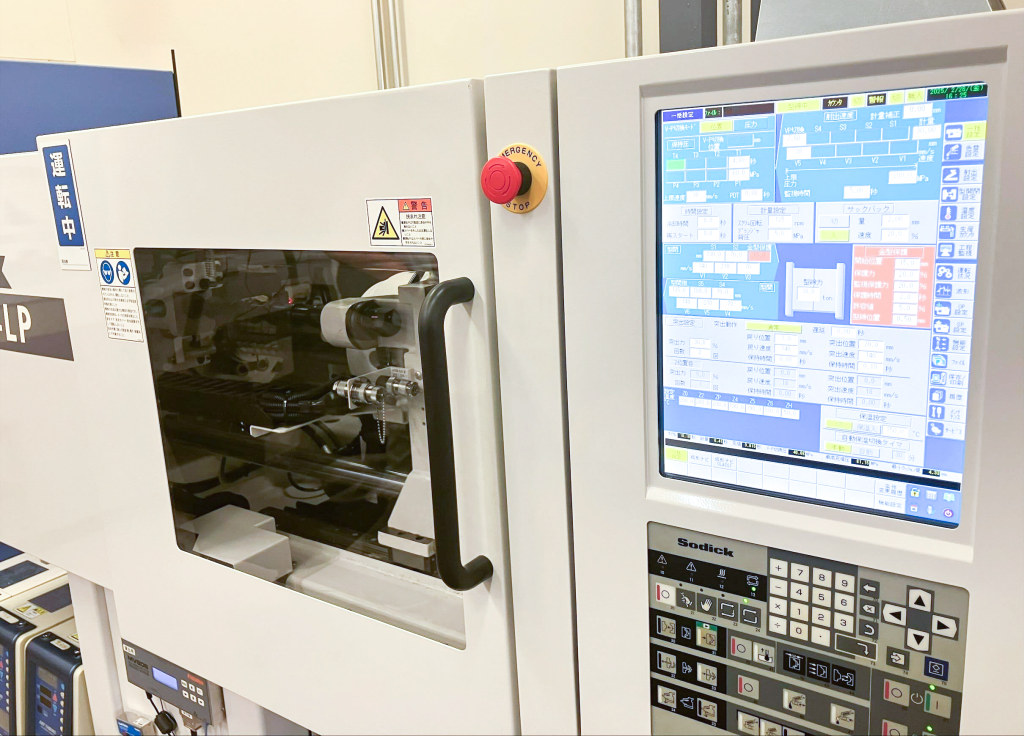
射出圧力と速度
樹脂の射出圧力や速度は充填状態に大きく影響します。射出圧力が低かったり射出速度が遅すぎるとショートショット(充填不足)やウェルドラインが発生し、高すぎるとエアトラップやボイド(気泡)、バリの原因となります。適切な圧力でゆるみなく充填しつつ、金型内で樹脂の乱流やせん断発熱を起こさせないことが重要です。
保圧と保圧時間
射出直後、ゲートが固まるまでの間に追加で圧力をかけ続ける工程が保圧(2次圧)です。保圧が低いと、樹脂が冷える過程で成形品の体積が収縮してヒケやショート、内部空洞が発生します。一方、高すぎる保圧は金型に過度な負荷をかけ、バリや離型不良、金型の損傷につながります。
樹脂温度と金型温度
成形材料ごとに推奨溶融温度レンジがあり、そのレンジから外れると充填不良や劣化不良の原因となります。温度が低すぎると樹脂の流動性不足で充填不良になりやすく、高すぎると樹脂が分解して焼けが発生します。また、金型温度は製品の表面品質や寸法精度にも影響するため、均一な温度管理が必要です。
材料管理
原料となる樹脂(ペレット)の予備乾燥は、成形不良を防ぐために重要です。特に吸湿性のある樹脂は、水分が射出時に蒸発してシルバーストリークや気泡の原因となることに注意しなければなりません。成形前に規定時間に沿ってしっかり乾燥させ、成形途中でも適切な水分管理を行います。
不良診断のための実務チェックリスト
万全の予防策を講じても、不良がゼロになるとは限りません。不良が発生した際は、以下のチェックリストを活用して、原因を特定し、必要に応じて設計・金型・成形条件などの見直しや対策を行います。
設計に関するチェックリスト
- 肉厚設計: 製品の肉厚は適切か、急激な厚みの変化や極端な厚肉/薄肉部がないか確認する
- 抜き勾配: アンダーカットはないか、十分なドラフトが付いているか確認する
- ゲート位置・数: 充填不足やウェルドラインの位置から逆算し、ゲート配置の見直しを検討する
- パーティングラインと外観: 合わせ面の段差や目立つ位置のパーティングラインを確認する
金型に関するチェックリスト
- 金型合わせ面・型締め: 傷やゴミによる隙間がないか、型締力は適正かを確認
- 冷却系統・温度: 冷却ライン(水穴)の詰まりや冷却効率の低下がないか確認
- ガス抜き: ベント溝に樹脂カスやガスヤニによる詰まりがないか確認
- 摩耗・損傷: キャビティとコアの摩耗や腐食、スライド不具合の有無を確認、不具合がある場合はスライド摺動面などに摩耗防止のグリスを塗布する
成形条件に関するチェックリスト
- 温度設定と樹脂状態: シリンダ温度と金型温度、樹脂の乾燥状態を確認
- 射出・保圧プロファイル: 射出速度や保圧のタイミング、圧力レベルを確認
- サイクルタイムと冷却: 冷却時間が適切か、成形時間が安定しているかを確認
- 設備・環境: 成形機や付帯設備の不調や環境変化(温度・湿度)がないかを確認
金型内計測システムの活用
成形不良の予防・改善には計測データに基づく客観的な分析が有効です。双葉電子工業の金型内計測システム(モールドマーシャリングシステム)は、金型内部にセンサを設置して樹脂の充填・固化挙動をリアルタイム計測します。本製品には次の特徴があります。
金型内計測システムの特徴
- 金型内センシングを低価格で導入できる
- 赤外線方式を採用し8msの高速な応答性を誇る樹脂温度センサをラインアップ
- 国内外で多数の販売実績
- 個社別のウェビナー・相談会やスクールを常時開催しておりサポート体制が充実
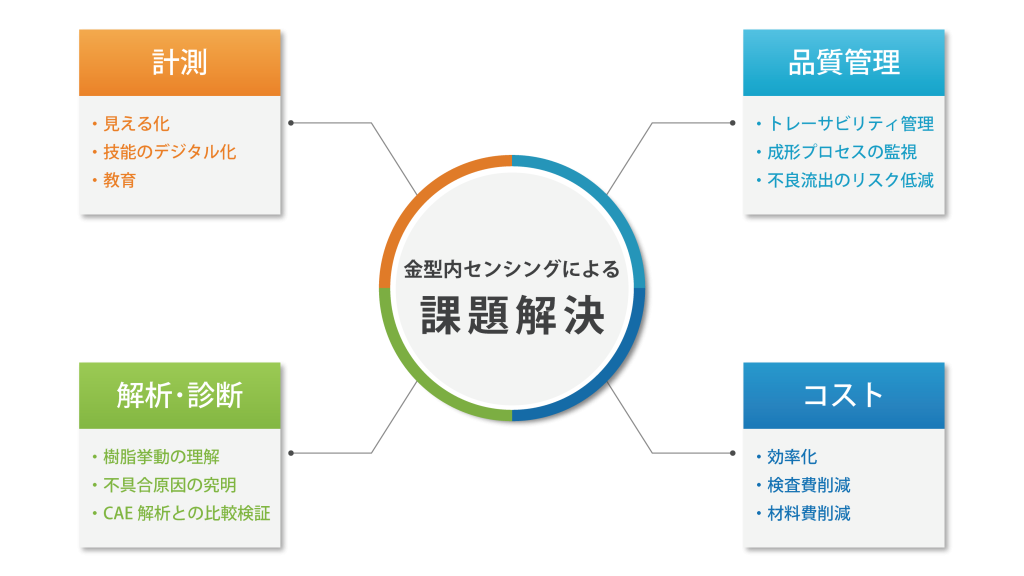
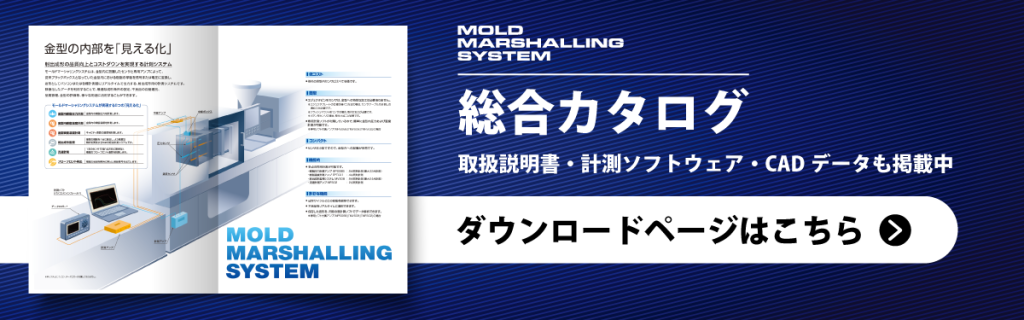
さらに最新の「射出成形AIシステム」では、センサデータとAI技術を組み合わせて以下を実現します。
良否判定機能
成形中に発生する様々な不良(ショートショットやバリなど)をセンサ波形から自動検知し、OK品/NG品を判定します。本機能により、成形中に金型内で起きている現象をより正確に捉え、不良かどうかをタイムリーに仕分けできるため、後工程での検査工数を大幅に削減できます。人手では難しい微妙な変化もAIがパターン認識して判断するため、従来見逃していた不良の兆候も捉えることが可能です。
成形条件調整機能
成形中のプロセスデータを常時モニタリングし、良品を成形できる条件をAIが提示・フィードバックします。環境変化や経時変動で成形状態が変わっても、システムが自動で最適条件の範囲を示すため、連続した不良品の発生を未然に防止できます。言わば経験豊富な技術者の勘所をAIが肩代わりし、誰でも安定した成形条件を維持できるようサポートしてくれる機能です。
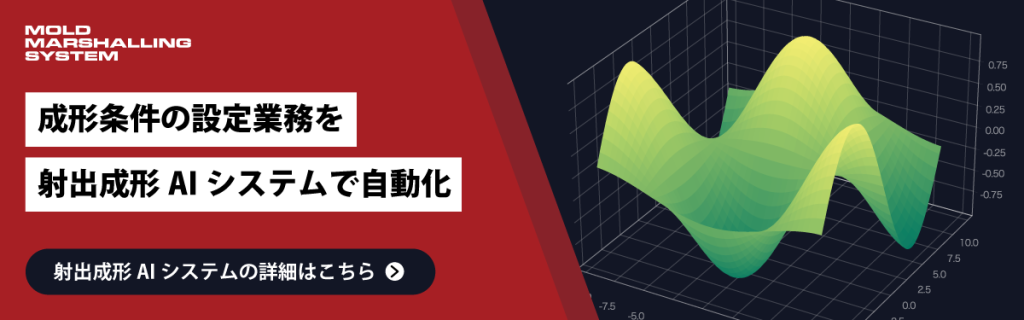
成形不良対策には予防措置と計測データの活用が効果的
射出成形における不良をゼロに近づけるには、製品設計・金型設計・成形条件設定のすべてで品質を作り込む統合的アプローチが必要です。設計段階での予防策に加え、金型内計測やAI技術を活用すれば、従来は熟練者の勘と経験に頼っていた成形条件の調整を熟練者でなくても調整できるようになります。
日々の生産でトラブルが発生したら原因を丁寧に突き止め、予防策を積み重ねる地道な努力が重要です。その先に不良率の低減、品質向上、コスト削減、顧客満足の向上という成果が待っています。設計・金型・成形条件・検査の各側面から自社プロセスを見直し、不良ゼロに向けた改善活動にお役立てください。